battery cell balancing / CCS-PCB
battery | cell | CCS | Nickel tab | PCB | balancing
Nickel tab PCBs for battery cell balancing (CCS)
Cell balancing PCBs or CCS-PCB (“Cell Connection System” or “Cell Contacting System”) are flexible circuit boards to which nickel tabs are soldered to enable later connection and management of individual battery cells. They protect the batteries, extend their lifespan, and optimize their capacity. Nickel tabs offer the optimal connection between a printed circuit board (PCB) and a battery, as they can be both soldered with tin and welded using various techniques. Nickel tabs are therefore the first choice and a key component of the ongoing revolution in electromobility.
Standard nickel tabs are 0.20 mm or 0.30 mm thick and consist of over 99% nickel, depending on the alloy. Their shape can be almost freely chosen, but overly narrow sections should be avoided to prevent breakage.
Advantages of Cell Balancing (CCS Boards) from Leiton:
- Longer battery life
- Maximum efficiency and safety
- High precision through controlled resistances
- 100% measurement and logging
- 100% traceability with QR code IDs
Especially during the testing phase, the additional setup costs for metal tools can significantly impact budgets. For cost-effective prototype production, we offer various standard nickel tabs and an economical manufacturing process:
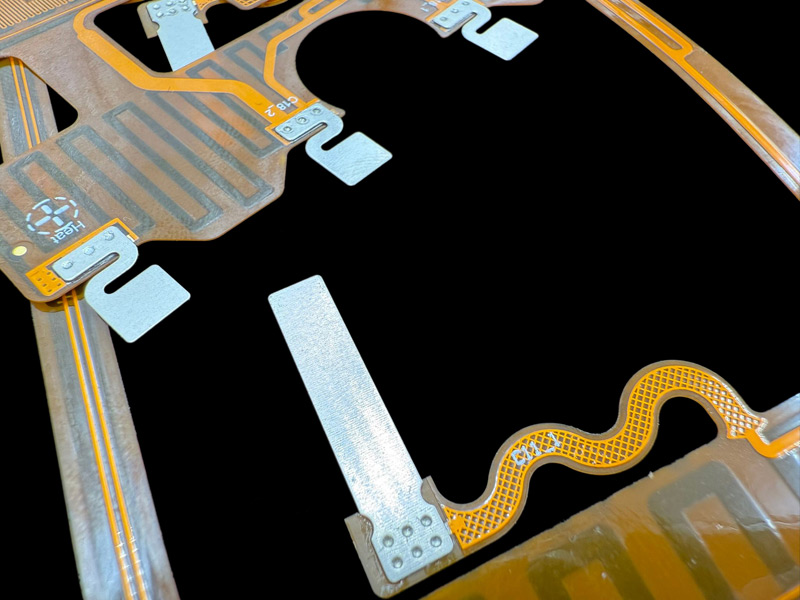
For optimal contact and stability of the nickel tabs, perforations are recommended to allow the tin to flow through them, thereby reinforcing the connection. A simple surface soldering without holes is significantly less stable. For the holes, diameters of 0.80 mm to 1.0 mm are recommended to ensure optimal tin flow.
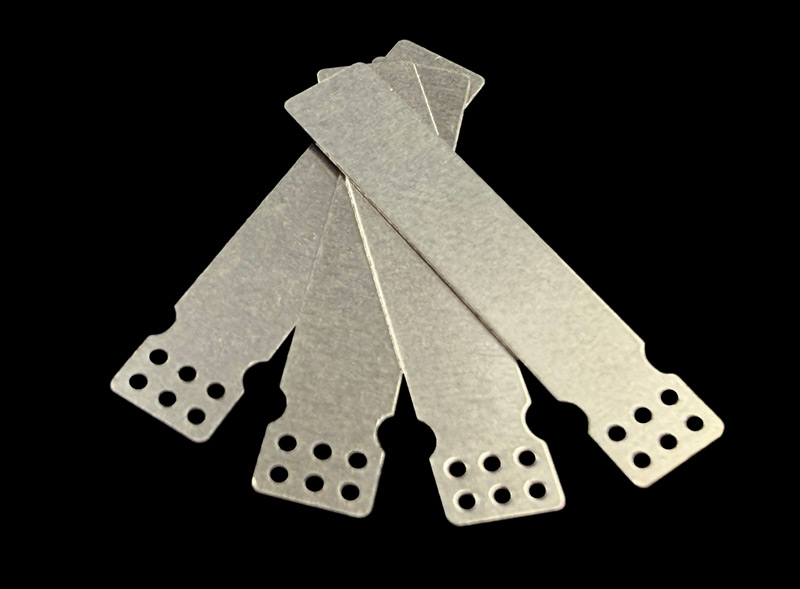
However, perforating the nickel tabs requires additional drilling, which is performed prior to stamping. This process incurs higher setup costs due to the tooling and equipment, especially for the stamping tool.
For prototypes, there is a more cost-effective alternative, though it comes with certain drawbacks (explained below). In this more economical method, neither stamping nor drilling is used; instead, the tabs are produced using strip cutting. This requires an approximately 0.4 mm wide slot for the 1 mm tin feed-through. Depending on the available space, multiple such solder feed-throughs can and should be included on the nickel tabs at the points where the connection to the PCB will later occur.
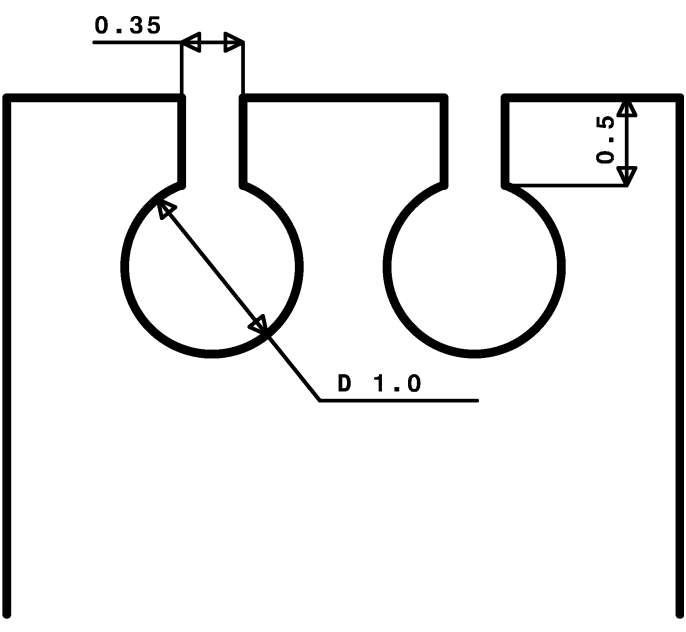
This relatively cost-effective method is primarily suitable for the prototype phase, where geometries and functionalities are being tested. It is less suitable for stress testing and has aesthetic drawbacks due to the strip-cutting process, such as scorch marks, burns, and uneven contours.
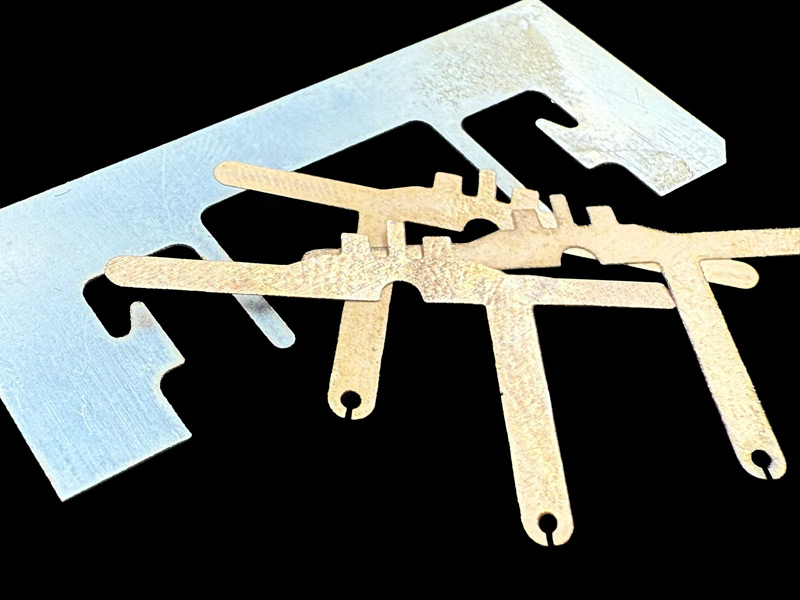
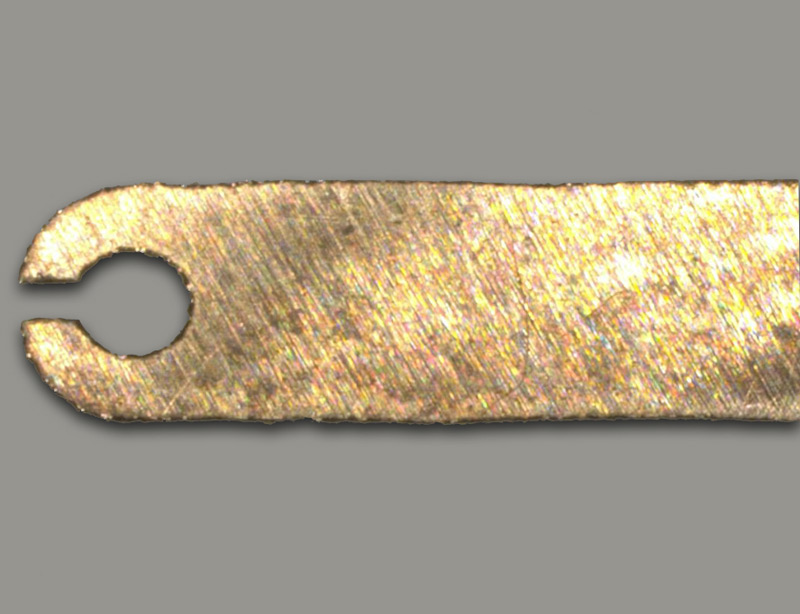
Leiton offers a variety of solutions for EV cell-balancing PCBs:
- Manufacturing of custom nickel tab geometries
- Cost-effective solutions for prototypes
- Online calculation of nickel tabs
- Soldering on flexible PCBs using fixtures to prevent shifting or twisting
- Support for extra-long flexible PCBs
- Additional assembly of connectors and components (commonly NTCs) on the FPC
- Testing, resistance measurements, documentation, and ID tracking with 100% traceability
- Flex-to-rigid connections using the Hot-Bar method
- Comprehensive consulting based on extensive expertise and numerous EV-FPC projects in layout, assembly, design, and testing
since 2021
- CO2 neutral through compensation
- Circuit boards – green on the outside, also on the inside
- Expertise through active exchange
- Expertise through training and further education

- ISO 9001:2015 Quality Management
- ISO 14001:2015 Environmental Management
- UL for rigid FR4 PCBs
- UL for flexible circuit boards
- UL for aluminum IMS boards