Hot-Bar Soldering | Flex | Starr | Starrflex
Flex to Starr Soldering - a cost-effective alternative to Starrflex.
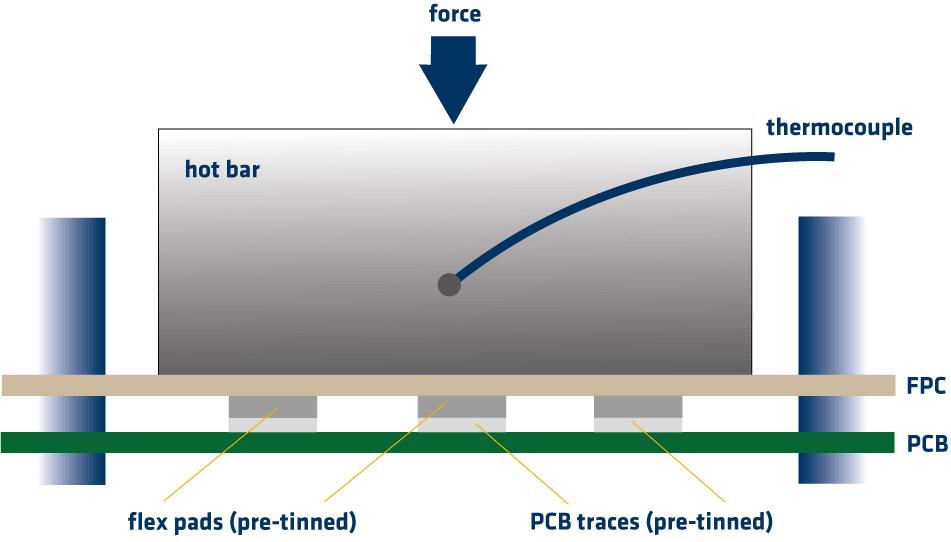
Modern EV battery technologies often require extremely large flexible printed circuit boards (PCBs). These are often equipped with NTCs (Negative Temperature Coefficient thermistors) and serve to monitor heat development across the entire battery – often over lengths of one meter or more. When it is necessary to transition these flexible PCBs into a rigid PCB, there are initially two options. Firstly, one can use conventional ZIF/LIF connectors. However, these have the disadvantage of not being fail-safe over time and requiring a certain height. Additionally, they may introduce transition resistances that are undesirable. The second option is to manufacture a rigid-flex PCB, but at this size, it would represent a significant cost factor.
The third, economical, and sustainable solution is the process of "Hot-Bar Soldering". In this process, the flexible PCBs and the rigid PCBs are separately and inexpensively manufactured. They are then soldered together using the Hot-Bar soldering method. This creates a permanent, stable connection between the flex and rigid that is flat, firm, and virtually resistance-free.
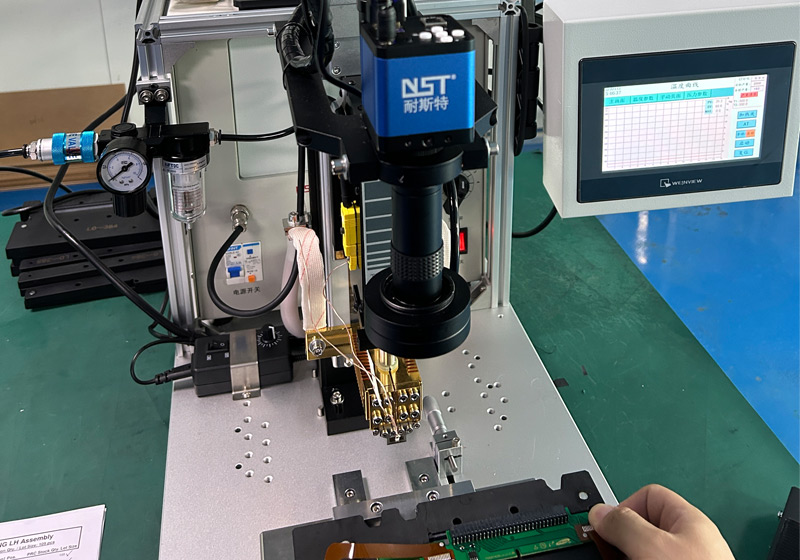
For precise alignment, appropriate adapters are manufactured. Existing holes in the circuit boards are used for alignment whenever possible. In the case of flexible circuit boards, additional positioning tabs with holes can be added, which are later removed.
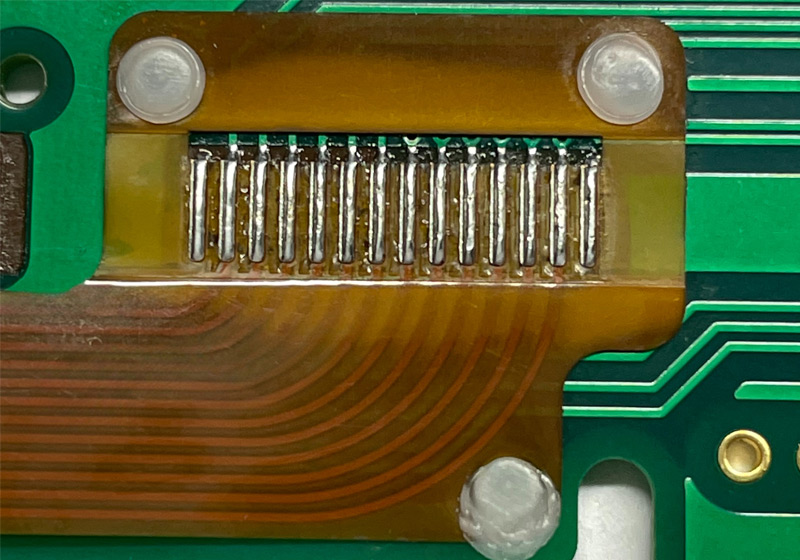
To mechanically secure against shear and tensile forces, additional plastic pins can be inserted through the flexible and rigid PCB and fixed in place.
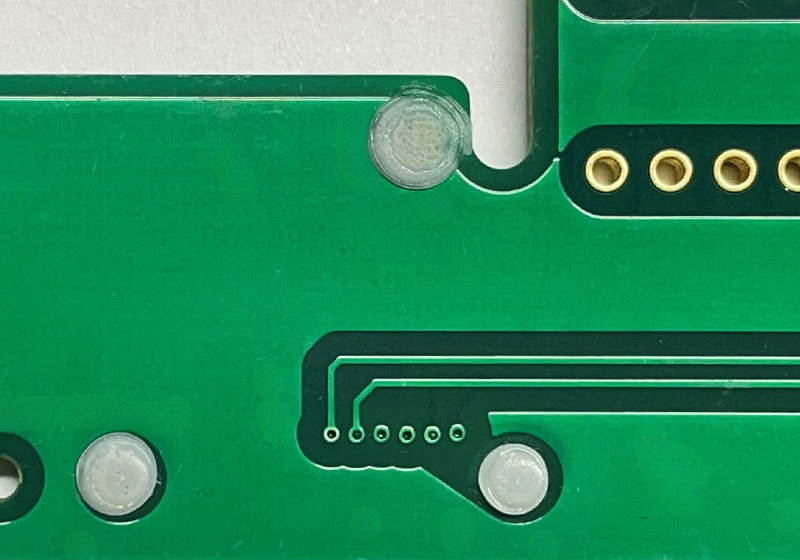
Instead of pins, a slightly flexible adhesive can also be used to additionally relieve the connection points. A transparent, UV-curing, semi-flexible adhesive is used for this purpose.
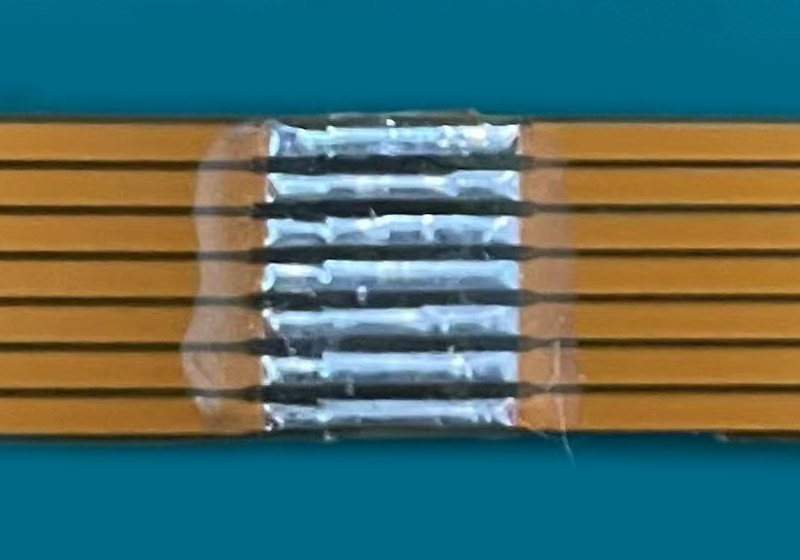
since 2021
- CO2 neutral through compensation
- Circuit boards – green on the outside, also on the inside
- Expertise through active exchange
- Expertise through training and further education

- ISO 9001:2015 Quality Management
- ISO 14001:2015 Environmental Management
- UL for rigid FR4 PCBs
- UL for flexible circuit boards
- UL for aluminum IMS boards