VIA Plugging | Tenting | Filling | IPC 4761 | PDF1 | PDF
Via Plugging, Tenting & Filling according to IPC 4761 as PDF overview in comparison
The IPC-4761 standard provides guidelines and definitions for the processing and handling of vias on printed circuit boards (PCBs). This standard describes various methods for sealing, covering and filling vias, which play an important role in the performance, reliability and processability of a PCB.
The three most common methods are explained below: plugging, tenting and filling.
Overview Via Plugging, Tenting & Filling according to IPC 4761
Definition: Plugging describes the complete or partial sealing of vias with a material such as solder resist or special pastes. This method is used to prevent contamination, solder bridges or other undesirable effects during the manufacture and use of the PCB.
- Protection of vias from contamination by liquids (e.g. during soldering processes or cleaning).
- Prevention of solder loss during through-hole plating.
- Improvement of the thermal and electrical properties of the PCB.
Typ III:
Plugged Via: The vias are sealed but not additionally coated with solder resist.
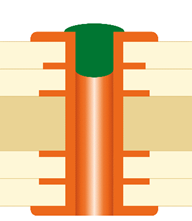
Type III-a: one-sided
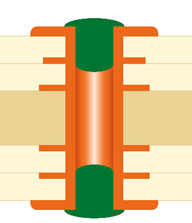
Type III-b: on both sides
Typ VI:
Plugged & covered Via: The vias are sealed and additionally covered with solder resist.
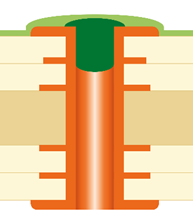
Typ VI-a: one-sided
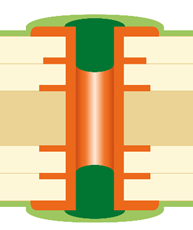
Typ VI-b: on both sides
Advantages:
- Prevents the penetration of solder during soldering.
- Provides a smoother PCB surface.
Disadvantages:
- Any chemical residues from production can be trapped in the vias when sealed on both sides and cause corrosion in the long term.
- Trapped air can escape from the vias during the soldering process and burst like bubbles. This technique should therefore not be used for vias that are placed under components.
Typical materials:
- Solder mask.
- Special resins or conductive pastes.
Overview Via Plugging, Tenting & Filling according to IPC 4761
Definition: During filling, the vias are completely filled with a resin. This method ensures that the vias are completely sealed and allows them to be covered by components.
- For high density interconnect (HDI) boards to create a flat surface that can be used for component placement or tracing over vias.
- Improving mechanical stability.
- Minimize the risk of delamination or defects due to thermal stress.
Typ V:
Filled Via: The vias are filled with non-conductive material. The process is largely uncommon for vias and is only used for buried cores.
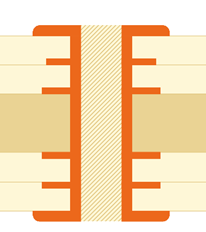
Typ V: Filled Via
Typ VI:
Filled and Covered Via: The vias are filled with non-conductive material and then covered with solder resist. The process is largely uncommon.
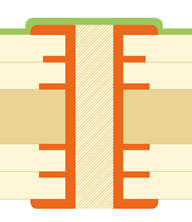
Typ VI-a: solder resist on one side
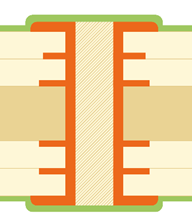
Typ VI-b: solder resist on both sides
Typ VII:
Filled and capped via: The vias are filled with material and then sealed with copper. In rare cases, conductive paste can be used.
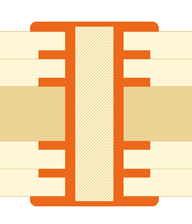
Typ VII: Filled and Capped Via
Advantages:
- Greater reliability under mechanical and thermal loads.
- Creation of a smooth surface for subsequent production steps such as component assembly.
- Protection against moisture and chemical influences.
- For type VII, solderability on the vias sealed with copper caps, therefore frequently used for BGAs.
- Can also be filled with conductive paste (high minimum application values and relatively expensive)
Typical filling materials:
- Non-conductive resins.
- Conductive pastes or resins, usually enriched with copper (High minimum application values! Expensive!)
Overview Via Plugging, Tenting & Filling according to IPC 4761
Definition: In tenting, the vias are completely covered with a tenting film.
- The process is rarely used nowadays due to its unreliability.
Advantages:
- Low cost.
Disadvantages:
- Tenting can crack under thermal or mechanical stress.
- Typ I: Tented Via: The via is covered on both sides by foil, but remains hollow on the inside.
- Type I-a: with foil on one side
- Type I-b: with foil on both sides
- Typ II: Tented and Covered Via: n addition to the cover, the via is protected by a copper layer.
- Type II-a: with foil and solder resist on one side
- Type II-b: with foil and solder resist on both sides
Overview Via Plugging, Tenting & Filling according to IPC 4761
The IPC-4761 defines different via types depending on processing and treatment:
Type | Method | Description |
---|---|---|
I | Tented Via | Via covered with dry film, hollow/open inside. |
II | Tented and Covered Via | Via covered with dry film and additional solder resist, hollow/open inside. |
III | Plugged Via | Via sealed with resin, hollow/open inside |
IV | Plugged & Covered Via | Via sealed with resin and additionally coated with solder resist, hollow/open inside |
V | Filled Via | Via completely sealed with resin, without copper lid. |
VI | Plugged and Capped Via | Via completely sealed with resin and additionally with solder resist, without copper cover. |
VII | Filled, Plugged, and Capped Via | Via completely filled and fitted with copper lid. |
The choice of the right method (plugging, tenting or filling) depends heavily on the specific requirements of the application. Criteria such as mechanical strength, environmental influences, electrical requirements and costs play a role in the decision.
- Tenting: Only for low-cost PCBs with minimal requirements for mechanical stability or environmental influences. No longer available from Leiton due to unreliability.
- Plugging: Recommended when protection from solder or liquids is the focus, but complete sealing is not required. Also suitable for vacuum pick-ups in the assembly process.
- Filling: Ideal for high-density PCBs and applications that require maximum reliability and stability.
since 2021
- CO2 neutral through compensation
- Circuit boards – green on the outside, also on the inside
- Expertise through active exchange
- Expertise through training and further education

- ISO 9001:2015 Quality Management
- ISO 14001:2015 Environmental Management
- UL for rigid FR4 PCBs
- UL for flexible circuit boards
- UL for aluminum IMS boards