IMS PCB | Leiterplatte | Alu | Board | Platine
IMS PCB Leiterplatten (Alu Board Platinen)
Alu-IMS - Wenn es bei Elektronik heiß hergeht!
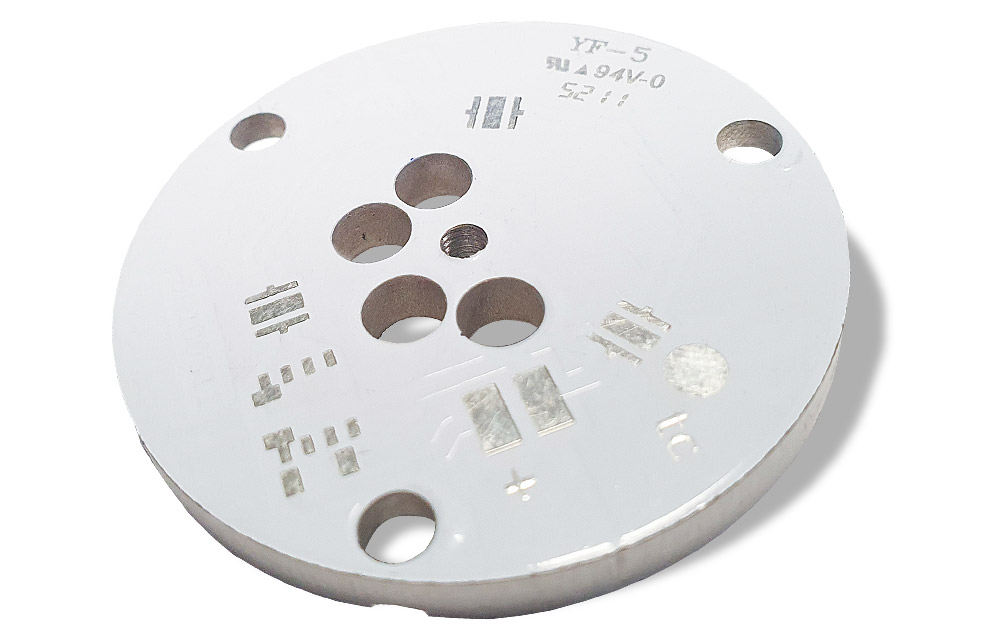
Der einstige Exot, die “Alu-Leiterplatte” oder “IMS-Platine” ist, unter anderem Dank der LED-Revolution im Lampenbereich, längst zu einem Standardprodukt geworden.
“IMS” steht hierbei für “Insulated Metal Substrate”, also isoliertes Metallsubstrat. Überall, wo high-power LEDs viel Wärme abstrahlen, spielen Aluminium-Platinen ihre Stärken aus, leiten Hitze ab und sorgen für längere Lebensdauer durch weniger Stress in der Anwendung.
Doch auch Standardprodukte bringen neue Herausforderungen mit sich, und die Anforderungen an Alu-Leiterplatten steigen stetig mit den immer höher gesetzten Zielen für Hochleistungselektronik und Wärmemanagement. Längst gehen die Anwendungen für Aluminium-Basis-Platinen weit über die reine Beleuchtung hinaus - High-Power-Heat-Management ist überall in der Elektronik angekommen!
Kühlen Kopf bewahren - mit IMS-Wärmemanagement
Die Herausforderungen liegen zum einen in den mechanischen Anforderungen, denn oft müssen Aluminiumplatinen exakt mit Kühlkörpern erweitert werden und die Alu-Platine bildet nur einen integrierten Teil des Wärmemanagements. Tiefenfräsungen oder Senkbohrungen sind übliche, mechanische Erweiterungen für eine bessere Integration in der fertigen Baugruppe. Anforderungen bezüglich immer höherer Lagenanzahlen bilden die zweite Front, an der Alu-Leiterplatten immer komplexer werden.
So wird die 1-seitige standard-Alu-Platine, mit dem Aluminium als Träger auf einer Seite, bei 2- oder mehrlagigen Leiterplatten als Alu-Kern hergestellt. Die Aluminium-Lage wird also in den Aufbau integriert. Mit den nötigen Isolierungen für Durchkontaktierungen sind hier nicht nur diverse Design Rules zu beachten, sondern auch bei der Herstellung ist besonderes Know-how gefordert, um solch unterschiedliche Materialien miteinander effektiv und hochwertig miteinander zu verbinden.



Optionen |
---|
Materialeigenschaften | 1 bis 12 W/mK, 38-100µm Isolation |
Materialhersteller | Ventec, BOYU, Polytronics, TCLAD (Bergquist) |
Materialdicken | 0,5 mm bis 3,0 mm |
Maximale Leiterplattengröße | 428 x 568 mm², weitere Übergrößen auf Anfrage |
Kupferdicken | 35µm / 70µm |
Lagenzahl | 1 bis 2 Lagen, Multilayer (Träger oder Kern) |
Oberflächen | HAL-bleifrei, HAL verbleit, ENIG, ENEPIG, OSP |
Mechanische Bearbeitung | Fräsen, Ritzen, Sprungritzen, Senkbohrungen, Stanzen |
Bohroptionen | Isolierte Bohrungen |
Metallisierungen | keine |
Lötstopp | Lack, Hochreflektionslack, Abdeckfolie (Coverlay) Coverlay-Farben: gelb, weiß, schwarz Lackfarben: grün, gelb, weiß, schwarz, Sonderfarben, Matt-Lacke |
Sonderlacke | Bestückungsdruck, Abziehlack, UV-Reflektionslack, Karbondruck |
Sondertechnologien | Mehrlagen Alu-IMS als Träger- und Kern-Variante, IMS in Überlängen über 1000 mm |
Qualitätsmanagement & Zertifizierungen | ISO 9001, ISO 14001, UL, IPC2/IPC3, IATF 16949, EMPB, VDA2, PPAP, Schliffe, Vermessungen, Konformitätserklärungen, Datenblätter, ESD-Verpackung uvm. |
Logistik | Rahmenaufträge, Konsignationslager, Abruflager, See-Luft-Split-Aufträge, Expressfertigung ab 2AT |
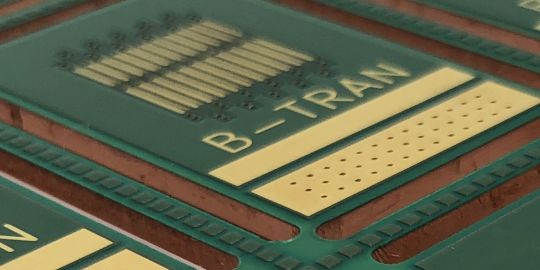
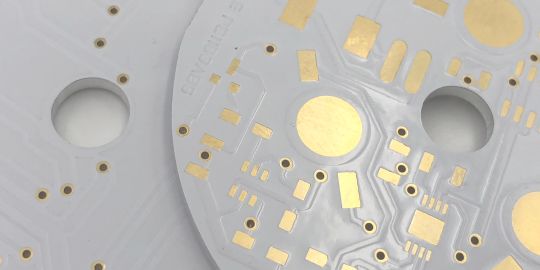
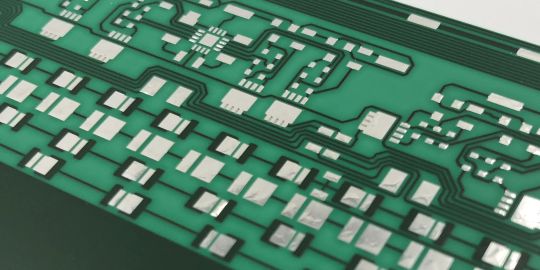
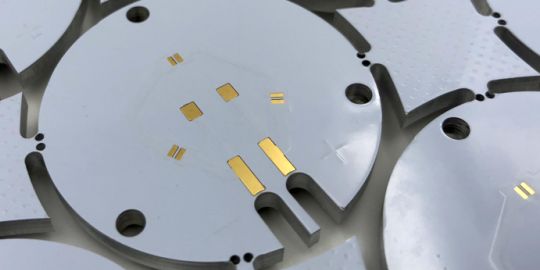
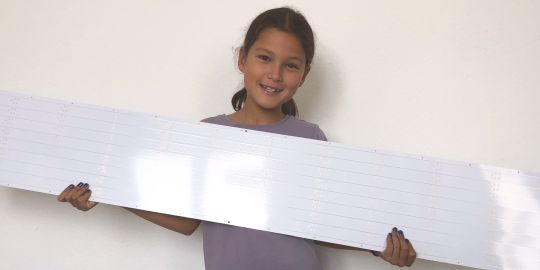
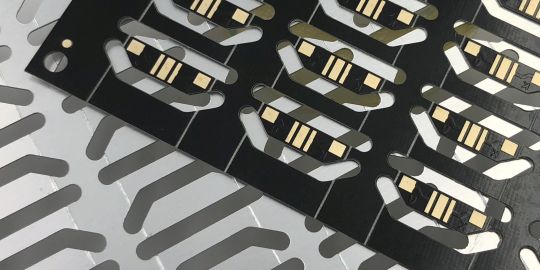
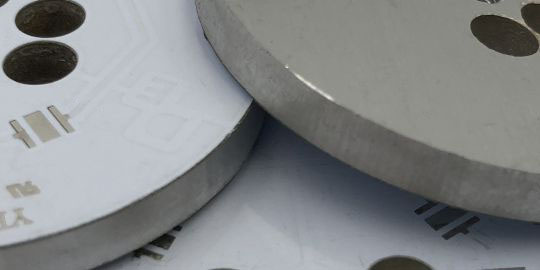
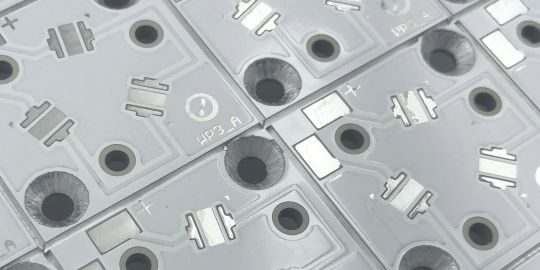
Definition: IMS PCB
IMS PCB steht für “Insulated Metal Substrate Printed Circuit Board”, also isolierte Metall-Substrat-Leiterplatte. Da Leiterplatten elektronische Komponenten verbinden und elektrische Ströme geleitet werden, ist die Isolation zum Aluminiumträger wichtig, da dieser sonst alles kurzschließen würde. Hierfür werden spezielle, gut wärmeleitende Prepregs verwendet. Diese bestehen aus Epoxidharz-Glasfasergewebe und Füllstoffen, die eine Wärmeableitung verbessern sollen.
IMS PCB funktionieren am besten, wenn der Wärmeleitwert dieser Isolationsschicht hoch ist. Durch einen hohen Wärmeleitwert kann die auf der Leiterplatten durch elektrische Ströme entstehende Hitze, optimal durch die Isolationsschicht auf den Aluminiumträger abgeleitet werden. Dieser Effekt sorgt für eine passive Kühlung der Elektronik.
Vorteile von IMS Leiterplatten & Alu-Platinen
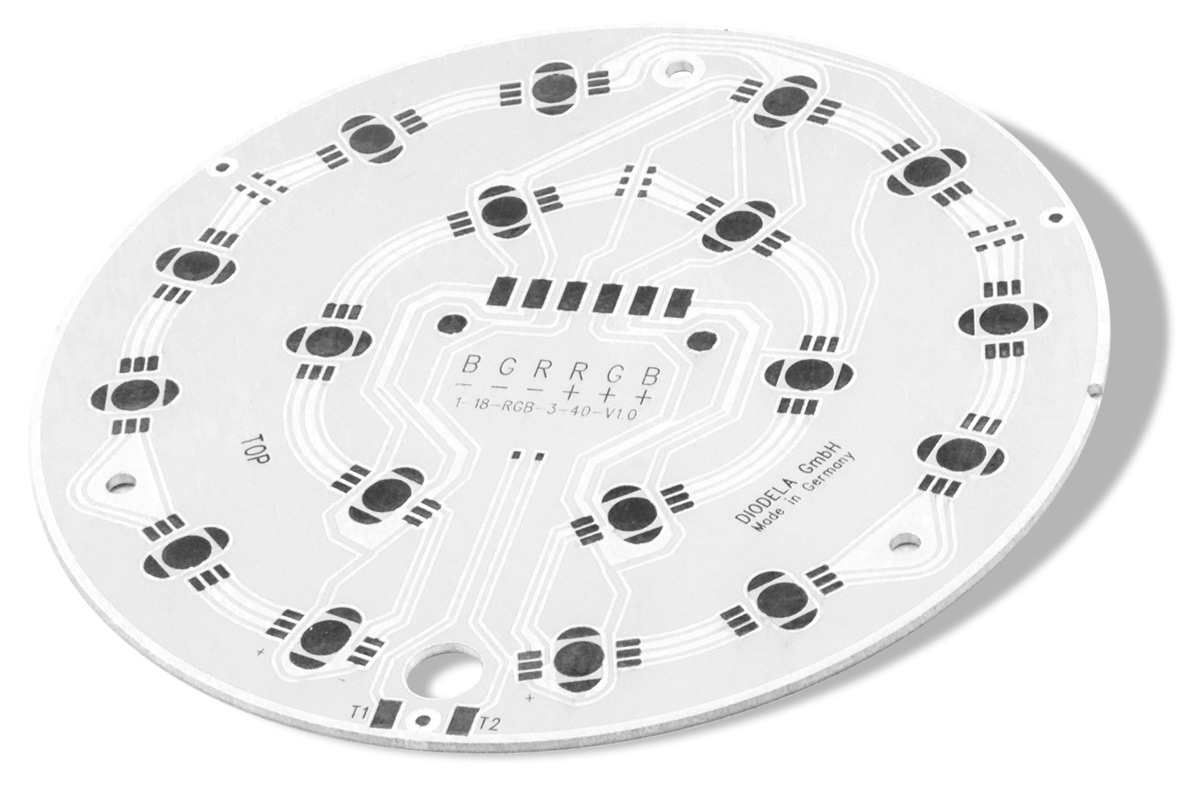
Die Vorteile von IMS Leiterplatten liegen in der Fähigkeit, große Hitze von Bauteilen abzuleiten. Hitze kann Bauteile zerstören, oder den Alterungsprozess stark beschleunigen. In extremen fällen können sich Bauteile im Betrieb durch die Hitze selbst entlöten, das Zinn wird also wieder flüssig und das Bauteil fällt ab, wodurch die Elektronik defekt ist.
Vorteile von IMS-Leiterplatten:
- Leitet Hitze effizient von Bauteilen ab
- Reduzierter Stress auf Baugruppen erhöht Lebenszeit
- Wärmeleitwert kann dem Bedarf angepasst werden
- Kostengünstige Herstellung der Platine
- Leichtes Material
- Bildet optimalen Übergang zu weiteren aktiven oder passiven Kühlmethoden
Die technische Performance von Aluminium-IMS-Leiterplatten kann in einigen Fällen durch die Verwendung von Kupfer-IMS-Leiterplatten noch übertroffen werden, da der Wärmeleitfähigkeit von Kupfer mit ca. 360 W/m*K noch mal deutlich über Aluminium liegt (ca. 220 W/m*K).
Anwendungsmöglichkeiten von IMS PCB
Herkömmliche Anwendungsbereiche für Aluminium IMS Platinen kamen ursprünglich aus der Beleuchtungsindustrie. Alu-Leiterplatten erfuhren durch das aufkommen sogenannter Power-LEDs einen großen Schub, da diese eine sehr große Hitze abgesondert haben. Heutzutage sind selbst Power-LEDs oft deutlich effizienter und geben weit weniger Hitze ab als noch vor einigen Jahren. Die Beleuchtungsindustrie kehrt daher oft von reinen IMS-PCB bereits wieder zu herkömmlichen, günstigeren FR4-Leiterplatten zurück.
In der Automobilindustrie finden IMS-Leiterplatten häufig Anwendung in der Motorsteuerung, welche nah an oder sogar innerhalb des Motors selber verbaut werden. Die sehr hohe Hitze des Motors kann so über die größere Fläche der Aluminium-Leiterplatte effektiver auf angeschlossene Wärmemanagementelemente abgeleitet werden.
Weitere Anwendungen sind Power-Elektronik, wo extreme Hitze durch die Schaltung selbst entsteht und durch IMS-Leiterplatten Wärme ohne weitere Wärmefallen abgeleitet wird. Auch bei Solid State Relays (SSR), wird die entstehende Hitze über die IMS-Platine direkt auf das Gehäuse abgeleitet, wodurch es zu einer passiven Kühlung kommt.
Arten von IMS Leiterplatten
IMS-Träger vs. IMS-Kern
Wie alle Leiterplatten unterscheiden sich auch IMS-Platinen zunächst einmal in der Lagenanzahl. Während die große Mehrheit an IMS-PCB zwar einlagige Aluminium-Träger-Platinen sind, kommen immer häufiger auch mehrlagige Schaltungen hinzu. Wenn mehrlagige FR4-Platinen auf einen Aluminiumträger gepresst werden, so redet man gemeinhin von z.B. 2- oder 4-Lagen Alu-Träger-Leiterplatten. Wird das Aluminium jedoch innerhalb des Multilayers oder der 2-lagigen Platine verbaut, so redet man von Aluminium-Kern-Leiterplatten.
Bei IMS-Träger-Leiterplatten ist der Herstellungsprozess der einzelnen Leiterplatten zwar vermeintlich einfach, jedoch kann es durch die Asymmetrie des Aufbaus zu Verwölbungen kommen. Der Prozess des Verpressens muss daher perfekt beherrscht werden.
Bei IMS-Kern-Leiterplatten steckt das Know-how hingegen im Vorbohren und Isolieren der späteren Durchkontaktierungen, so dass diese einerseits nicht den Metallkern treffen und kurzschließen, andererseits aber nicht zu großzügig isoliert und damit der wärmeableitende Effekt reduziert wird.
Weitere interessante Sondertechnologien rund um IMS-Leiterplatten und vieles mehr finden Sie hier.
Wärmeleitwert und TG der Isolation
Ein weiteres Merkmal ist allgemein das verwendete Isolations-Prepreg. Während normales FR4 einen Wärmeleitwert von ca. 0,4 W/m*K hat, beginnen die Isolations-Schichten von IMS-Alu Leiterplatten bei 1,0 W/m*K. Bis ca. 3,0 W/m*K ist handelsüblich. Höhere Wärmeleitwerte bis zu 12 W/m*K sind bei vielen Herstellern selten aber in unserer Onlinekalkulation verfügbar.
Der TG von Alu-IMS liegt meist zwischen TG120 und TG185 bei TCLAD-Material (Bergquist). Der Grund für die Wahl eines sehr niedrigeren TG120 für die Isolationsschicht erscheint unüblich, liegt aber in den unterschiedlichen Wärmeausdehnungskoeffizienten von dem Aluminiumträger und der Kupferschicht begründet. Durch einen niedrigeren TG120 wird die Isolationsschicht früher “nachgiebig”, was Spannungen im gesamten Aufbau reduziert und die Baugruppe bei höheren Temperaturen entlastet. Ein vermeintlicher Nachteil kann unter Umständen zu einem Vorteil werden.
Aluminium PCB vs. Kupfer PCB
Die letzte große Unterescheidung von IMS-Platinen ist das verwendete Metallsubstrat. Während Aluminium in den Elektronik-Anwendungen wegen der niedrigen Kosten und dem geringen Gewicht zwar klar dominiert, gibt es auch Kupfer-IMS-Leiterplatten. Ein Vorteil von Kupfer-IMS-Leiterplatten ist zudem, dass eine leitende Verbindung zum Metallträger über eine Durchkontaktierung hergestellt werden kann. Dies ist mit Aluminium-IMS nicht möglich. Auch können Alu-IMS-Platinen nicht mit chemisch Zinn hergestellt werden, da das Aluminium die Chemie im Zinnbad verunreinigt. Mit Kupfer-IMS ist dies hingegen problemlos möglich.
Herstellung unserer IMS-Leiterplatten & Platinen
Konventionelle 1-lagige IMS-Leiterplatten gleichen in der Herstellung Großteils der Produktion von normalen 1-lagigen FR4-Platinen. Die größten Unterschiede liegen in der mechanischen Bearbeitung, da sowohl beim Bohren als auch beim Fräsen langsamer als bei FR4 gearbeitet werden muss. Werden besondere Parameter für die mechanische Bearbeitung nicht eingehalten, so kommt es schnell zu Gratbildung. Weitere Besonderheiten entstehen bei chemischer Vergoldung (ENIG oder ENEPIG), da hierbei das Aluminium überall abgeklebt werden muss, um den Kontakt mit dem Goldbad zu verhindern, welches dadurch verunreinigt werden kann.
Größere Unterschiede zur konventionellen Platinenfertigung gibt es in der Herstellung von 2- oder mehrlagigen IMS-Kern-Leiterplatten, bei denen das Aluminium innerhalb der Leiterplatte eingebettet ist. Hierfür muss die reine Aluminiumlage an den Stellen der späteren Durchkontaktierungen größer vorgebohrt und dann mit einer Paste isoliert werden. Diese vorgebohrte Aluminiumlage wird dann im Multilayer verpresst und die Durchkontaktierungen werden durch die isolierten Bereiche hindurchgebohrt, um Kurzschlüsse zum Aluminium-Kern zu vermeiden.
Günstige Aluminium IMS PCB Leiterplatten direkt vom Hersteller online kaufen
Aluminium-Platinen mit vielfältigen Optionen aus professioneller, industrieller Herstellung finden Sie in unserer Onlinekalkulation. Neben unterschiedlichen Wärmeleitwerten, Material- und Kupferdicken, sowie diversen Lötstoppfarben gibt es verschiedenste Terminoptionen. Auch das beliebte TCLAD (Bergquist) HPL Material mit nur 38µm Isolation ist in unserer Onlinekalkulation verfügbar!
IMS steht für “Insulated Metal Substrate” (deutsch: isoliertes Metallsubstrat) und bezeichnet Leiterplatten mit einer integrierten, aber elektrisch isolierten Metalllage (meist Aluminium, selten auch Kupfer). IMS-Leiterplatten haben aufgrund des integrierten Metalls eine deutlich höhere Wärmeleitfähigkeit als FR4-Platinen und finden meist Anwendung, wenn in der Elektronik selbst oder in der Umgebung sehr hohe Temperaturen entstehen. Durch das bessere Wärmemanagement von IMS-Platinen erhöht sich bei sinnvollem Einsatz die Lebensdauer der Elektronik teils erheblich.
IMS-Leiterplatten kann man sowohl nach dem verwendeten Metall unterscheiden (Aluminium oder Kupfer), als auch nach der Position der Metalllage im Lagenaufbau. Liegt das Metall außerhalb (kontaktierbar), spricht man von IMS-Träger-Leiterplatten. Wurde das Metall im Lagenaufbau innerhalb der Platine verpresst, so spricht man von IMS-Kern-Platinen. Das Metall ist dann nur an den Kanten sichtbar, aber nicht von einer Seite vollständig kontaktierbar.
Aluminium-IMS-Leiterplatten haben in Elektronikanwendungen mit hoher Hitzeentwicklung diverse Vorteile gegenüber konventioneller FR4-Leiterplatten:
- Wärme wird von Bauteilen abgeleitet
- Dadurch verringert sich der Stress auf die Elektronik und die Lebenszeit verlängert sich
- Wärmeleitfähigkeit kann nach Anforderungen höher gewählt werden
- Aluminium-IMS-Platinen sind sehr kostengünstig, da weit verbreitet
- Aluminium ist ein sehr leichtes Material
- Das Aluminium kann mit Wärmeleitpaste o.ä. direkt auf den überleitenden Kühlkörper montiert werden
IMS-Leiterplatten unterscheiden sich primär im verwendeten Basismaterial. Während herkömmliche Leiterplatten aus einem Epoxidharz-Glasfasergewebe (genannt “FR4”) bestehen, haben Aluminium-IMS-Leiterplatten eine Basis aus einer gängigen Aluminium-Legierung (z.B. AL5052 mit >3% Magnesiumanteil). Die Dicke dieser Aluminium-Basis entspricht üblicherweise den gängigen Leiterplattendicken von 0,8mm oder 1,5mm. Zwischen diesem Aluminiumträger und dem Kupfer liegt eine isolierende Epoxidharzschicht mit Wärmeleitfähigkeiten, die meist über das Standard FR4 mit 0,4 W/mK hinausgehen. Üblich sind hier 1,3W/mK oder 2,0W/mK und 3,0W/mK. Höhere Wärmeleitwerte sind selten aber bei Leiton bis 12,0W/mK auch in der Onlinekalkulation verfügbar.
Durch die Aluminiumschicht einer IMS-Leiterplatte wird Hitze um ein Vielfaches effizienter von sogenannten Hot-Spots abgeleitet und über die breite Fläche der Aluminiumschicht verteilt. Hot-Spots sind gefährlich, wenn bestimmte Bauteile in ihrer Anwendung eine sehr hohe Hitze entwickeln. Solche Hitze kann das Bauteil nachhaltig schädigen oder sogar dazu führen, dass dieses Bauteil sich selbst entlötet. Im Allgemeinen steigern IMS-Alu-Leiterplatten in Anwendungen mit extremer Hitzeentwicklung die Lebensdauer der Elektronik teils erheblich. Besonders effizient werden Aluminium-IMS-Platinen, wenn auf die rückseitige Aluminiumlage noch weitere passive oder sogar aktive Kühlungen angeschlossen werden und die Hitze somit noch besser von der Schaltung abgeleitet werden kann.
Aluminium-IMS-Platinen kommen immer dann zum Einsatz, wenn es eines effizienten Wärmemanagements bedarf. Alu-IMS-Leiterplatten helfen dabei, Umgebungshitze oder Hitze, die durch die Elektronik selber entsteht, gleichmäßig über das Aluminium-Träger-Substrat zu verteilen und dadurch sogenannte “Hot-Spots” zu vermeiden. Hot-Spots, oder Hitze allgemein, verringern die Lebenszeit von elektronischen Bauteilen. So verdoppelt sich die Lebenszeit eines Elektrolytkondensators zum Beispiel, wenn die Temperatur im Spitzenbereich von 95°C auf 105° gesenkt wird. Übliche Anwedungsgebiete für Alu-IMS-PCB sind:
- (High-intensity)-LED-Schaltungen/Beleuchtung
- Power-Elektronik / Transformatoren
- Motorsteuerungen (in extremer Hitzeumgebung)
Kurz: Jein. IMS steht für “Insulated Metal Substrate”, also “isoliertes Metallsubstrat”. Damit stimmt der Teil des Wortes, wo “Metall” verwendet wird. Allerdings sagt die Abkürzung IMS nichts über die Lage des Metallsubstrates aus. Viele Hersteller verwenden fälschlicherweise den Term “Metallkern”, obwohl sie damit “Metallträger” meinen. Denn ein Kern befindet sich in der Mitte des Lagenaufbaus, während ein Träger sich an einer Seite befindet. Der maßgebliche Großteil an IMS-Leiterplatten besteht aus nur einer Kupferlage mit, durch isolierendem Prepreg getrenntem, Aluminium auf der anderen Seite und gehört damit strenggenommen zu Metallträger-Leiterplatten. Erst wenn das Aluminium innerhalb des Lagenaufbaus liegt (z.B. Kupfer-Isolation-Aluminium-Isolation-Kupfer) sollte man von einer Metallkernleiterplatte reden.
IMS-Aluminium-Leiterplatten kosten in der Regel etwas mehr als reine FR4-Leiterplatten. Im Prototypenbereich liegt dies meist an der geringeren Auslastung der Produktionsnutzen im Sharing-Prinzip (Kombination von verschiedenen Aufträgen auf einem Produktionszuschnitt), bei Serien liegt es an den leicht höheren Materialkosten von Aluminium im Vergleich zu FR4. Rein von der Verarbeitung sind 1-lagige FR4-Leiterplatten und Aluminium-IMS-Leiterplatten kostentechnisch nahezu identisch. Leicht erhöhter Aufwand (Kosten) entsteht jedoch bei Aluminium in den mechanischen Prozessen (Fräsen und Bohren), da hier langsamer gearbeitet werden muss und sich die Werkzeuge schneller abnutzen.
Aluminium-IMS-Basismaterialien unterscheiden sich in vieler Hinsicht. Am naheliegendsten sind neben der Gesamtdicke und Kupferschicht, die Dicke der Isolationsschicht (Prepreg) zwischen Aluminium und dem Kupfer, sowie dessen Wärmeleitwert. Generell gilt: je dünner diese Isolationsschicht und je höher der Wärmeleitwert, desto besser kann Hitze von der Kupferlage in das Aluminium abgeleitet werden. Achtung: Eine sehr dünne Isolation hat oft Nachteile bezüglich der Durchschlagsfestigkeit!
Weitere Unterschiede gibt es im Bezug auf den TG des verwendeten Prepregs. Aluminium und Kupfer können prinzipiell extrem hohe Temperaturen von mehreren hundert Grad aushalten, jedoch ist das schwächste Glied in der Kette diese Isolation. Der TG bei herkömmlichen Aluminiummaterialien liegt bei 130°C, womit sich eine maximale Betriebstemperatur von ca. 100°C ergibt. High-Performance Materialien wie z.B. TCLAD (Bergiquist) HPL-3015 hat einen TG185°C mit einer maximalen Dauerbetriebstemperatur von 140°C.
Wie die Bezeichnung schon sagt, liegt der größte Unterschied im verwendeten Material. Was aber bedeutet das für die technische Leistung der jeweiligen IMS-Leiterplatte? Vorteile von Kupfer-IMS-Leiterplatten liegen vor allem in dem noch höheren Wärmeleitwert des Metalls (Kupfer: ~320W/mK versus Aluminium ~240W/mK). Das bedeutet, dass Hitze im Metallträger noch effizienter verteilt oder von Hot-Spots abgeleitet wird. Dieser Vorteil kommt jedoch mit einigen Nachteilen.
Zum einen wiegt Kupfer 9g/cm³) mit dem dreifachen deutlich mehr als Aluminium (2,8g/cm³), was in einigen Produkten bereits ein Ausschlusskriterium darstellt. Zum anderen bedeutet das höhere Gewicht von Kupfer, in Kombination mit generell doppelt bis dreifach höheren Rohstoffkosten als Aluminium, dass der Preis für eine gleichgroße Leiterplatte allein vom Rohstoff her um den Faktor 6 bis 10 ansteigt. Bedenkt man nun noch Faktoren wie Versandgewicht, Verbreitung (Verfügbarkeit), und dass Kupfer in der mechanischen Bearbeitung noch langsamer durch die Prozesse läuft, ergibt sich ein preislicher Aufschlag um Faktor 10 aufwärts, der mit dem Performancegewinn beim Wärmeleitwert vom Faktor 1,3 kaum im Verhältnis steht. Kupfer-IMS-Leiterplatten bleiben daher eine High-Tech-Variante, die nur in Betracht kommen, wenn die Aluminium-IMS-Technologie ausgereizt wurde.
Ein technologischer Vorteil von Kupfer-IMS-Leiterplatten liegt jedoch in der Möglichkeit, das Kupfer im Träger galvanisch mit Bohrungen zu verbinden (durchkontaktieren) oder auf dem Kupferträger zu löten. Beides ist mit Aluminium-IMS nicht möglich.
seit dem Jahr 2021
- CO2-neutral durch Kompensation
- Leiterplatten - außen grün, innen auch
- Expertise durch aktiven Austausch
- Expertise durch Schulung und Weiterbildung

- ISO 9001:2015 Qualitätsmanagement
- ISO 14001:2015 Umweltmanagement
- UL für starre FR4-Leiterplatten
- UL für flexible Leiterplatten
- UL für ALU IMS Leiterplatten